INFRASTRUCTURE
- Home
- Infrastructure
Sigma Melleable Infrastucture
For the last 35 years, spanning two generations, Sigma group has always endeavored to keep abreast with the Technology and provide an optimum solution to our customers. Continuing with this tradition, the group has embarked upon putting a new state-of-art foundry that specializes in producing High-quality Gray Iron and Ductile Iron castings with machine shop in Padavla, Rajkot.
Sigma’s infrastructure is designed and configured to meet the specific needs of the foundry’s operations, ensuring efficient production while prioritizing safety, environmental responsibility, and compliance with regulations.
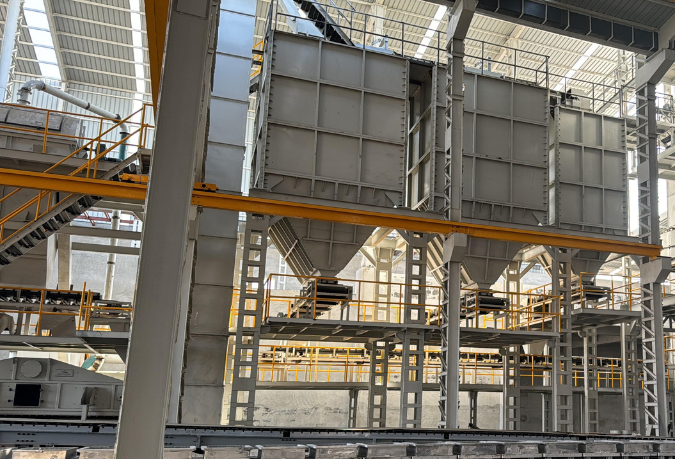
Sand Plant
- Our Sand Plant is equipped with sand multi-controller (SMC) which regulates and monitors the process in a sand mixture to ensure the characteristics of the prepared molding sand remain within the constant range and thus improve the mold quality and give the better surface finish of the casting
- Capacity 55 MT/Hr and storage capacity of 200 MT
- Moisture and additives added by three load cells that monitors and controls optimum max.
- We have incorporated ZSM Pull cord system in all belt conveyors for safety purpose.
Moulding Facility
SINTO JAPAN FBO N - III Features
- Single station design
- Squeeze horizontal Parting and Aeration
- Average max mold rate of 100 Mold/hr with core casting and 130 mold/hr without core casting
- Vertically no spill sand or strike - off sand
- No pits or bottom boards required
- Mold to Mold consistency
- Programmable hydraulic squeeze
- Box size - 510mm x 660mm x 120-200mm depth
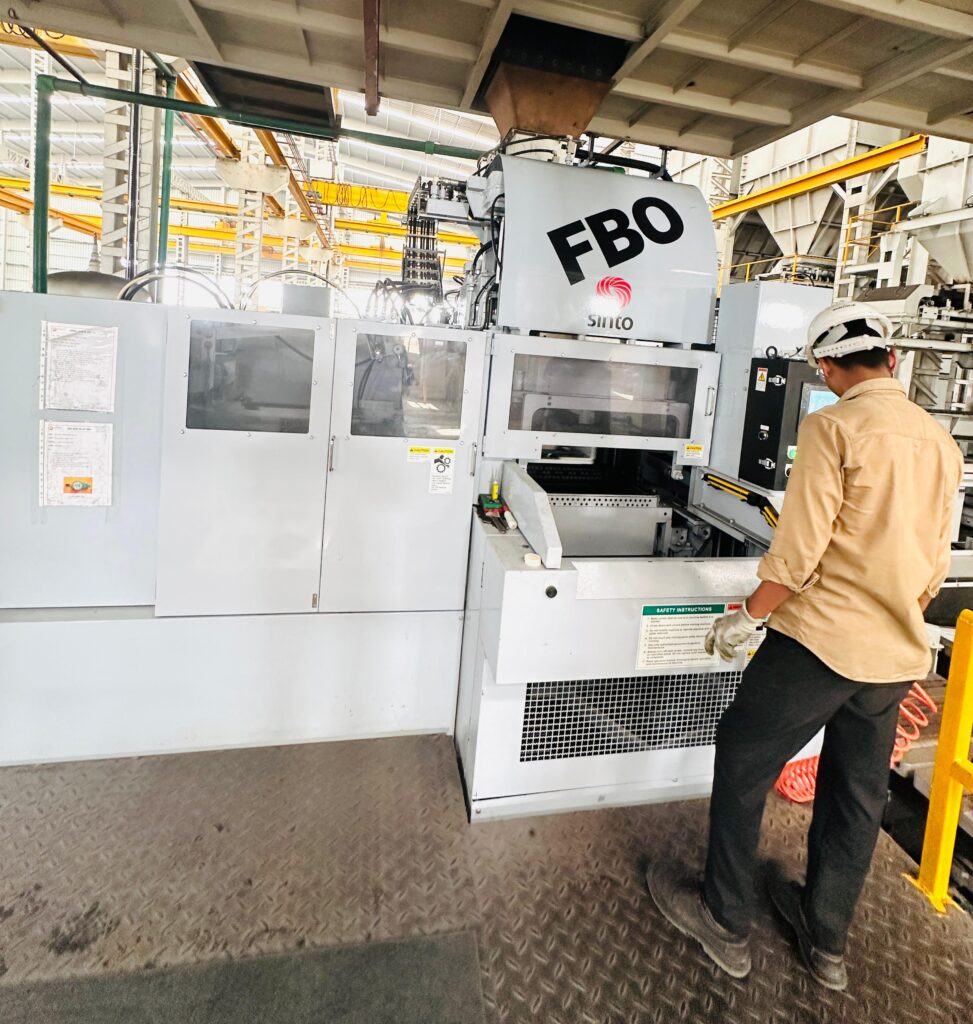
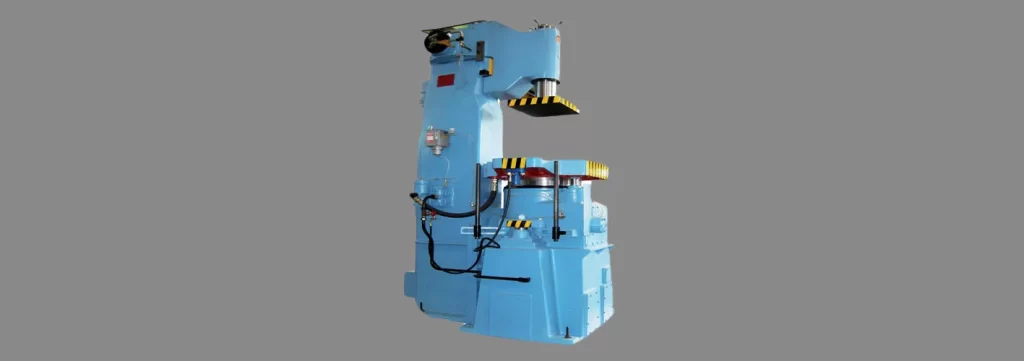
ARPA 450 & 900
Simultaneous Jolt Squeeze Moulding Machine Features
- Damage free stripping
- Hydro pneumatic swing in and out for fast productivity
- Adjustable pins to suit different box sizes
- Pneumatic timer for jolt and squeeze
- Box size (Arpa 450) – 18"x24", 20"x21", 26"x26", 26"x29", 29.5"x29.5" and Height 3" to 10"
- Box size (Arpa 900) – 33.5"x33.5", 39.5"x39.5", 43.5"x47.5" and Height 8" to 14"
Sand Core Shop
- "MAKE WELL" Cold core shooter 8 machines(25 Lt, 15 Lt, 10 Lt, 5 Lt Capacity) with blowing time varying between 30 Second and 2 minutes with one ton per hour sand mixture
- The core shooter can accommodate horizontally jointed core using amine as a curing agent with resin addition approximately 6500 cores per day
- Fully automatic operation by use of PLC with HMI
- Inbuilt gas generator with air as a carrier medium
- Automatic Hydraulic core ejection
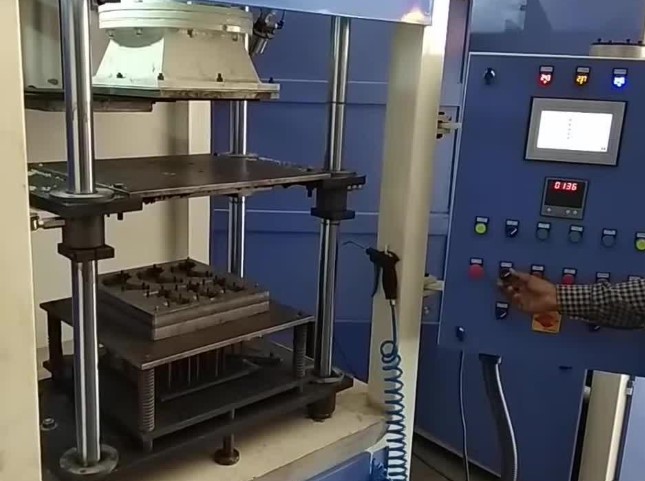
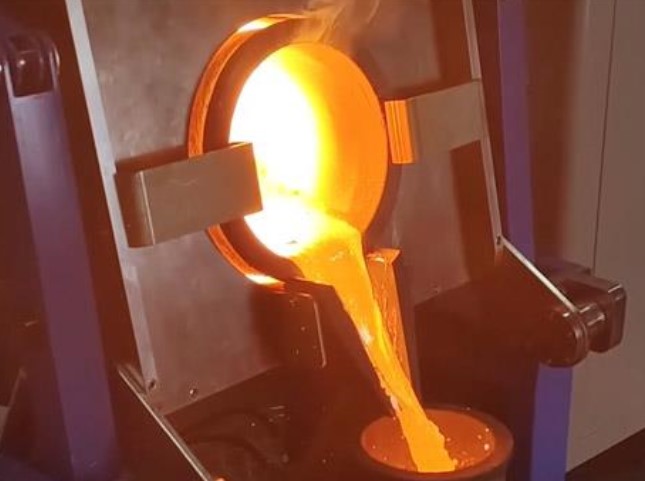
Melting
Melting Capabilities
- 30 MT Per Day Melting Capacity
- Dual track induction furnace 500 kg/hr - 2 Nos. & 750 kg/hr – 2 Nos.
- Tight chemistry control with complete traceability
- Customized software and control for efficient energy management
- Temperature monitor with data logger
- Emergency load response program and synchronous reverse program participant to reduce stress on the Power Grid
Machine Shop
Value Added Machine Shop
- CNC Turning Center: Ace Micrometric & LMW (CNC)
- Vertical Turning Lathe: Ace Micrometric (VTL)
- Vertical Machining Center Ace Micrometric (VMC)
- Turning Conventional Lathe
- Radial Drill Machine
- Pillar Drill Machine
- Tapping Machine
- Ultrasonic Cleaning Machine
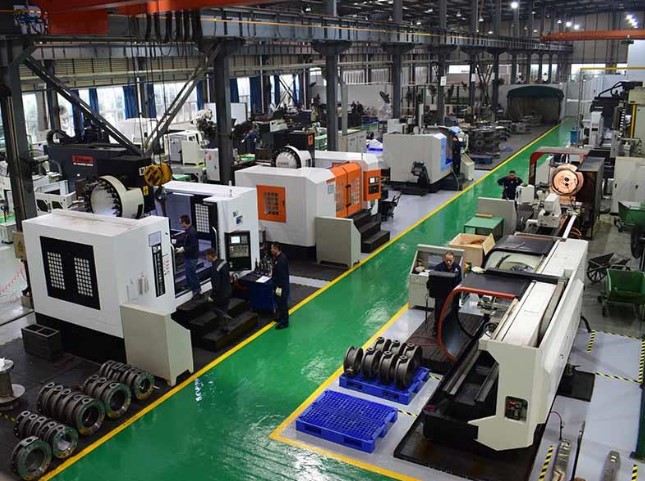
Facility Features
- 261300 Square feet land with 130000 Square feet manufacturing space with high bays and with modern lighting
- Training Hall
- Multiple conference room
- 5S implementation
- Canteen with staff quarters
People
- 225 Highly Skilled and qualified Employees
- Productive and motivated crafts people
- Professional team
- Leading-edge experts
- Strong work ethic management and team
- Team with good communication
Facilities
- Fully Automatic Sand Plant
- FBON III Sinto Flask less Automatic Moulding line
- Arpa 450 & 900 Moulding Machines
- 8 Fully Automatic cold core shooting machines
- Dual Track Induction Furnace 500 kg/hr – 2 Nos. & 750 kg/hr – 2 Nos.
- Metal Pouring by lifting crane
- Laboratory for sand
- Metrology for finished product
- Shotblasting & Fettling Facility
- Modern Painting Facility
Engineering
Through our design process. We identify how to make the job easier, less expensive and more efficient. Design resides, 3D modeling, solidification analysis and rapid prototyping are just a few of the service we offer.
Pattern Making
All the patterns are manufactured with the help of casting simulation software.
3D Software is used by engineers to assist them to visualize, analyze, and communicate the designs intent prior to an actual prototype or sample being created.
Production
Production Capabilities
- We can accommodate all varieties with small as well as high volume of parts
- Sizes: 1.0 kg to 180 kg Single Piece
- Capacity of 30000 MT per year
- Consistency in physical & meteorological Properties
- Design review, 3D Modeling and simulation capabilities
Metal We Cast
Grey Iron
India : FG100, FG150, FG200 & 250, FG300 & 350
USA : NO 25, NO 30, NO 35, NO 40, NO 45, NO 50
Ductile Iron
India : SG370, SG400, SG500, SG600, SG700
USA : 60-40-18, 65-45-12, 80-55-06, 100-70-03, 120-90-02
Silicon Molybdenum Cast Iron (SiMo)
Testing Facility
Metal Testing Lab
- Hardness testing
- Brinell hardness
- Spectro-meter with 19 element testing
- Universal tensile & elongation testing M/C
- Image Analyzer with microscope with built-in photo camera
- Carbon Silicone Analyser (CE Meter)
- Modularity Testing on Ductile Iron parts
NDT
- Magnetic particle is done by approved agency
- Dye penetrate testing
- Radiography testing is done by approved agency
Quality Control & Sand Testing Lab
- CMM (1200x1000x600mm)
- Surface roughness tester
- 2D Height Gauge
- Marposs Gauge for bore measurement
- Air Gauge for bore measurement with statistical process control
- Sand AFS no sieve testing
- Green sand compressive strength testing
- Green sand compactness testing
- Sand permeability testing
- Mold hardness testing
- Rapid sand moisture testing
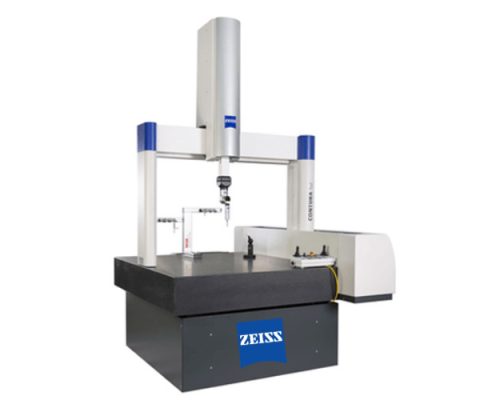
CMM - Zeiss
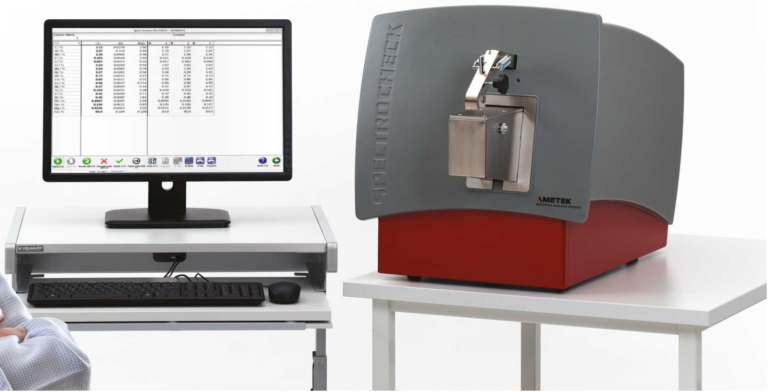
Spectrocheck - Ametek
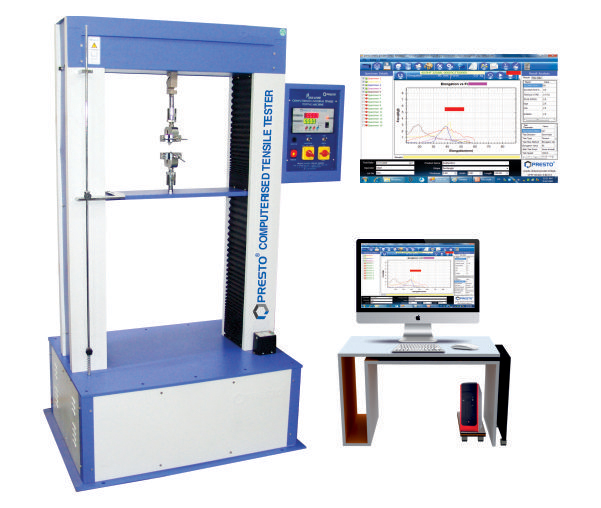
Tensile Tester - FIE
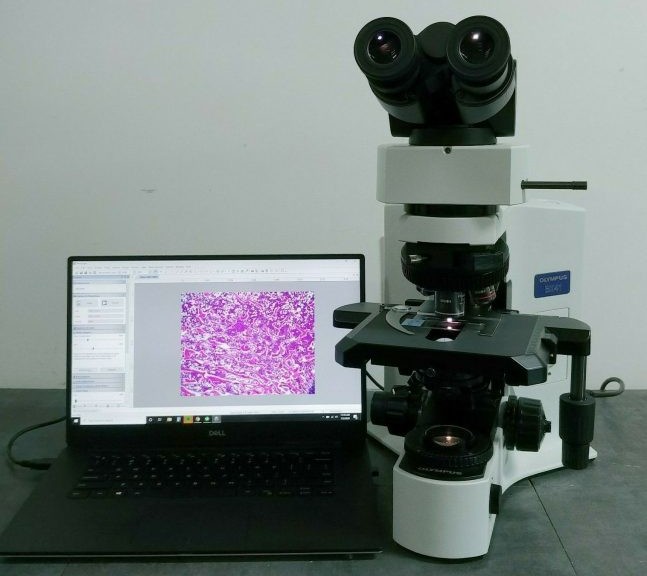